As the growing crisis around RAAC concrete in schools and public buildings dominates the national news, Catherine Croft provides a handy explainer on this widely used post-war building material. Any situation which might cause the sudden collapse of a...
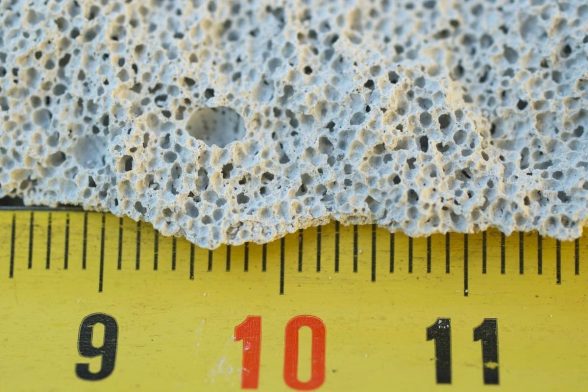
As the growing crisis around RAAC concrete in schools and public buildings dominates the national news, Catherine Croft provides a handy explainer on this widely used post-war building material.
Any situation which might cause the sudden collapse of a building is clearly enormously concerning, and the safety of people must be the top priority. There is an urgent need to understand where RAAC was used, to examine whether or not it is now failing in each case, and then work out how best to repair or replace every building which requires urgent attention.
We don’t know yet if any of the schools or other buildings with deteriorated RAAC are ones which are either listed, or ones which may have merited listing in the future, but heritage concerns must of course come second to public safety.
What is RAAC and why was it developed in the first place?
AAC is the acronym for “autoclave aerated concrete”, first developed in the 1920s, RAAC, is AAC with added steel reinforcement-hence the “R” at the front. AAC is a special form of pre-cast concrete, that is concrete made in a factory, rather than cast on site, like the very visible concrete of most Brutalist buildings, such as the South Bank Centre.
By aerating the mix to provide a bubbly structure, which has been accurately compared to an Aero chocolate bar, the overall weight of the concrete is hugely reduced. The aeration is caused by a chemical reaction initiated when water is added to the mix. RAAC is cast in steel moulds and then, after it has set sufficiently to be taken out, it is placed in an autoclave in the factory to increase its strength. This heats it under pressure, a process more like firing a clay brick in a kiln than the normal curing of concrete at ambient temperature.
Unlike standard concrete the RAAC mix only includes small particles, and no larger stone aggregate (the small pebbles or chippings which can give normal concrete much of its character). This means that the individual planks and blocks created are much lighter and therefore cheaper and easier to transport to site and lift into place. They also have other advantages, including better thermal insulation, and good sound insulation.
It has always been understood that RAAC elements have less compressive strength than regular concrete ones of the same size, that is they will crush more easily if a compressive or “squashing” load is applied to them. This will have been taken into account in the initial design process, and there seems to be no evidence that this was not the case in almost all instances. The most common use of RAAC was for beams, used in flat roof and floor construction.
Problems
There seem to be a number of specific types of problem emerging:
Problems relating to the original construction, such as RAAC beams which were never adequately supported at each end. Problems relating to poor maintenance, including roofs where the overlaying waterproofing has failed, causing the concrete beneath it to have been wet for a long period, and to have deteriorated.Other issues which may be problematic, include flat roofs where extra weight has been added to address problems of water ingress. It will also be crucial to take into account the strength of RAAC when adding additional insulation to a building to improve its thermal performance.
Beyond schools, it seems probable that other public buildings from the same period – like hospitals, prisons, libraries, theatres and leisure centres – may also contain various amounts of RAAC.
It has been said that all RAAC in the country has now “exceeded its design life”. This sounds drastic, but many building components exceed their design lives totally safely. It does not seem to have been proven that all RAAC inevitably crumbles apart after any fixed period of time, and estimating future “design life” when making a component, or building a building, is not a precise science. Research needs to be done on RAAC taking examples made by different manufactures, and used in a full range of building types and locations, with good and bad subsequent maintenance regimes.
Parallels
There may be parallels that can be drawn with High Alumina Cement concrete. This was a product popular from 1950 to 1970, but banned after a few well publicised collapses in the 1970s. Subsequent research has shown that the primary causes of these collapses were poor construction details or chemical attack, rather than problems with the concrete itself, and (as the Concrete Centre attests) up to 50,000 buildings with HAC continue to remain successfully in service today in the UK. The financial cost and the environment impact of replacing concrete can be immense, and no doubt there will also be some heritage buildings lost as part of a sensible and proportionate response to the RAAC crisis. But hopefully further research will be able to pinpoint exactly which sets of circumstances require demolition, and which can be addressed by remedial works and monitoring.
To reiterate: RAAC almost certainly will be found in buildings C20 cares about, but making sure everyone is safe must come before anything else.
Catherine Croft is the Director of the Twentieth Century Society and teaches the Conservation of Historic Concrete course at West Dean College.