We like drinking out of glass. In many ways, it’s an ideal material for the job. It’s hard-wearing, and inert in most respects. It doesn’t interact with the beverages you …read more
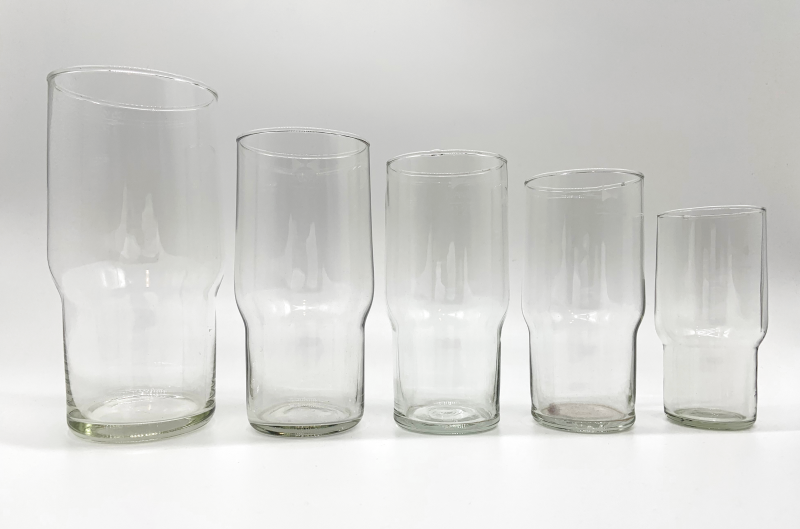
We like drinking out of glass. In many ways, it’s an ideal material for the job. It’s hard-wearing, and inert in most respects. It doesn’t interact with the beverages you put in it, and it’s easy to clean. The only problem is that it’s rather easy to break. Despite its major weakness, glass still reigns supreme over plastic and metal alternatives.
But what if you could make glassware that didn’t break? Surely, that would be a supreme product that would quickly take over the entire market. As it turns out, an East German glassworks developed just that. Only, the product didn’t survive, and we lumber on with easily-shattered glasses to this day. This is the story of Superfest.
Harder, Better, Glasser, Stronger
It all started in the German Democratic Republic in the 1970s; you might know it better as East Germany. The government’s Council of Ministers deemed it important to develop higher-strength glass. Techniques for the chemical strengthening of glass were already known by the 1960s, and work on developing the technology further began in earnest.
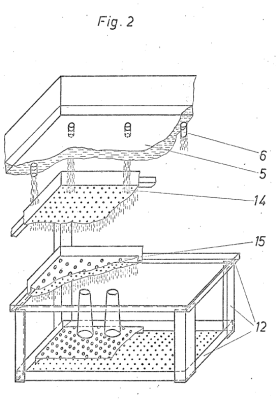
These efforts came to fruition in the form of a patent filed on the 8th of August, 1977. It was entitled Verfahren und Vorrichtung Zur Verfestigung Von Glaserzeugnissen Durch Ioenenaustausch—or, translated to English—Process and Apparatus for Strengthening Glassware By Ion Exchange. The patent regarded an industry-ready process, which was intended for use in the production of hollow glass vessels—specifically, drinking glassware.
The researchers understood that glasses typically broke in part due to microscopic cracks in the material, which are introduced in the production process. These microcracks could be mitigated by replacing the sodium ions in the surface of the glass with larger potassium ions. The larger ions thus cause a state of compression in the surface layer. Glass is far more capable of resisting compression rather than tension. The high compressive stresses baked into the material help resist tension forces that occur during impact events, thus making the material far more resistant to breakage.
The process of exchanging sodium ions in the glass with potassium ions was simple enough. The patent outlined a process for raining down a molten potassium salt solution onto the glassware, which would harden the outside surface significantly. This process was chosen for multiple reasons. It was desired to avoid immersing glassware into a huge bath of molten potassium salt, as the large bath of hot material would present safety hazards. There were also concerns that excessive time spent at high temperatures following immersion would lead to a relaxation of the crucial compressive stresses that built up in the glass from the ion exchange. Interior surfaces of the glassware could also be hardened by rotating the glasses on a horizontal axis under the “salt rain” so they were also exposed to the potassium salt to enable the ion exchange.
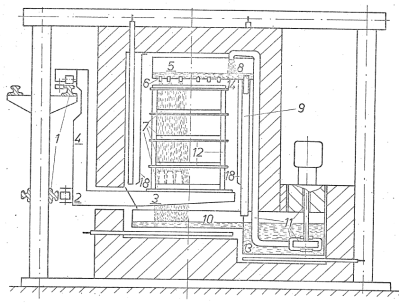
Recognizing the value of this patent, the Council of Ministers fast-tracked the technology into commerical production at the Sachsenglas Schwepnitz factory. The glassware was originally named CEVERIT, which was a portmanteau of the German words chemisch verfestigt—meaning “chemically solidified.” It also wore the name CV-Glas for the same reason. Production began in earnest in 1980, primarily centered around making beer glasses for hospitality businesses in East German—bars, restaurants, and the like. The glass instantly lived up to its promise, proving far more durable in commercial use. While not completely indestructible, the glasses were lasting ten to fifteen times longer than traditional commercial glassware.
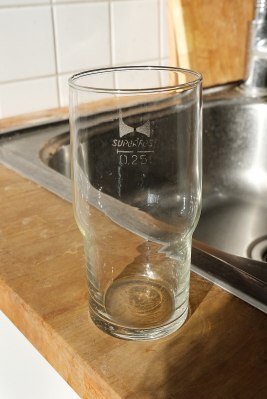
Despite the political environment of the time, there were hopes to expand sales to the West. On the urging of sales representative Eberhard Pook, the glasses were referred to by the name Superfest. The aim was to avoid negative connotations of “chemicals” in the name when it came to drinking glasses. Despite efforts made at multiple trade fairs, however, international interest in the tough glassware was minimal. Speaking to ZEITMagazin in 2020, Pook noted the flat response from potential customers. “We built a wall where we stacked the glasses… Look at it, it’s unbreakable!” says Pook, translated from the original German. “No reaction.” He was told that the material’s strength was also a great weakness from a sales perspective. “At Coca Cola, for example, they said, why should we use a glass that doesn’t break, we make money with our glasses,” he explained. “The dealers understandably said, who would cut off the branch they’re sitting on?”
Production nevertheless continued apace, with 120 million glasses made for the domestic market. Hardened glassware was manufactured in all shapes and sizes, covering everything from vases to tea cups and every size of beer glass. Stock eventually began piling up at the factory, as restaurants and bars simply weren’t ordering more glassware. Their chemically-strengthened glasses were doing exactly what they were supposed to do, and replacements weren’t often necessary.
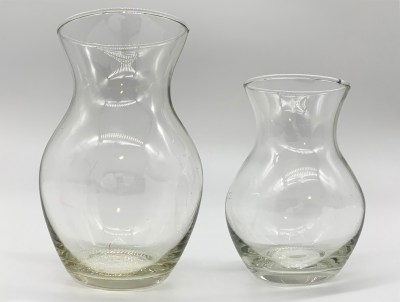
Regardless, the future was unkind to Superfest. Urban legend says that the reunification of Germany was the beginning of the end, but it’s not entirely true. As covered by ZEITMagazin, the production of Superfest glassware was ended in July 1990 because it simply wasn’t profitable for the company. Production of other glassware continued, but the chemically-hardened line was no more. The patent for the process was allowed to lapse in 1992, and pursued no more.
The question remains why we don’t have chemically-hardened glassware today. The techniques behind Superfest are scarcely different to those used in Gorilla Glass or other chemically-strengthened glasses. The manufacturing process is well-documented, and the world is full of factories that ignore any concept of intellectual property if there was even an issue to begin with. Indeed, a German crowdfunding effort even attempted to replicate the material—only to fall into insolvency this year.
It seems that either nobody can make stronger drinking glasses, or nobody wants to—perhaps because, as Superfest seemed to indicate—there simply isn’t any money in it in the long term. It’s a shame, because the world demands nice things—and that includes beer glasses that last seemingly forever.
Featured image: “Superfest glasses in five sizes” by Michael Ernst